Pharma Supply Chains and Untapped Opportunities
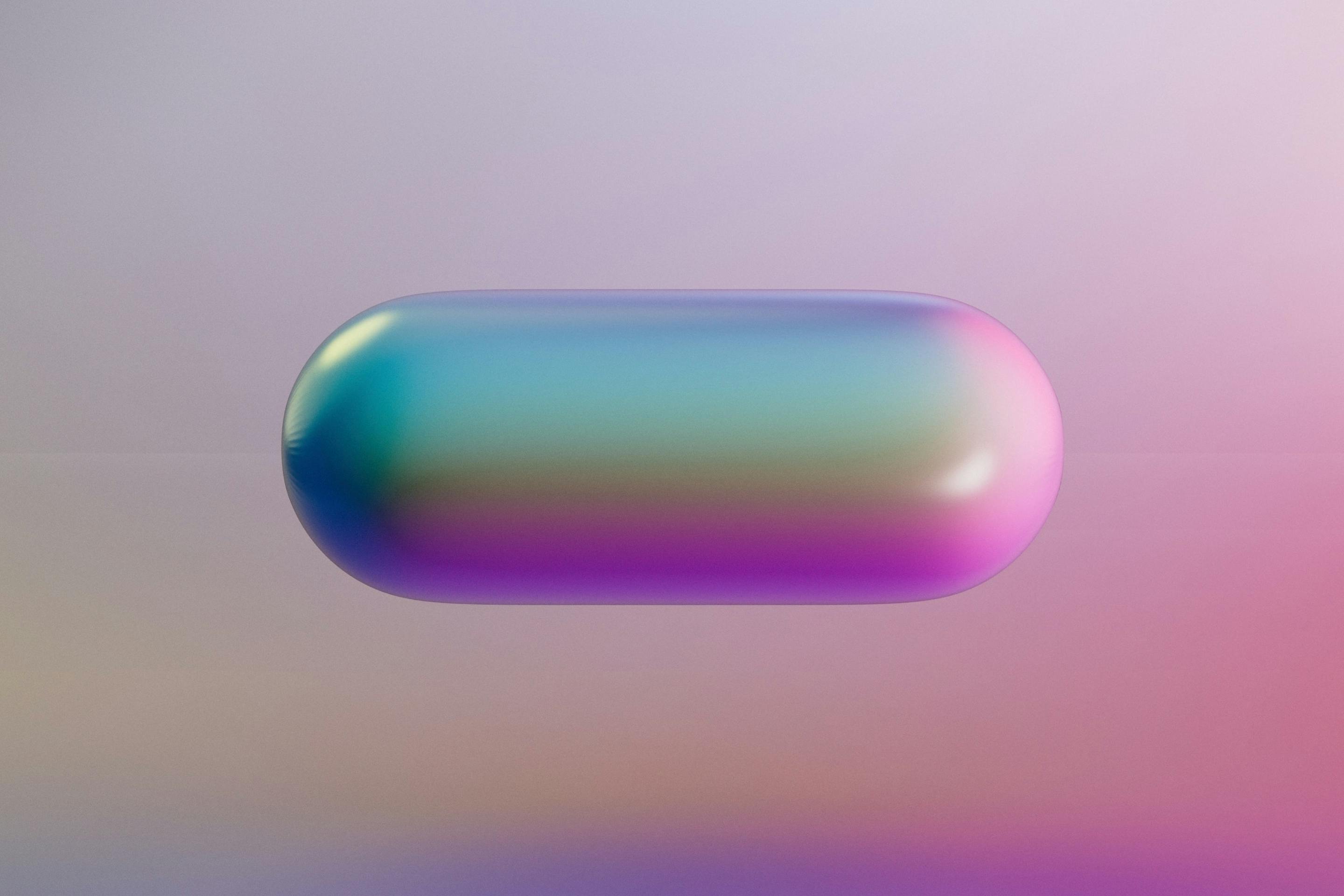
The Pharma Supply Chain: An Overview
The pharmaceutical industry has experienced significant growth in recent years. At the end of 2019, the total global pharmaceutical market was valued at $1.25 trillion. This is a sizable increase from 2001 when the market was valued at just $390 billion. Understanding the multi-dimensional driving forces of the market, and its underpinning supply chains illustrates how people obtain medications and what influences the price at which they purchase them.
Global pharmaceutical logistics and supply chains are characterized by their increasing complexity due to a number of internal and external parameters shaping this highly-regulated industry. In the past, the majority of pharma investment was spent on the discovery, development, and marketing of new drugs and therapeutics.
Fast forward to today and the greatest challenge facing pharma companies is the effective management of supply chains. Underinvestment in pharma supply chains has led to unpreparedness in large-scale shifts in demand, new product types with complex requirements, and rising pressure from industry regulators.
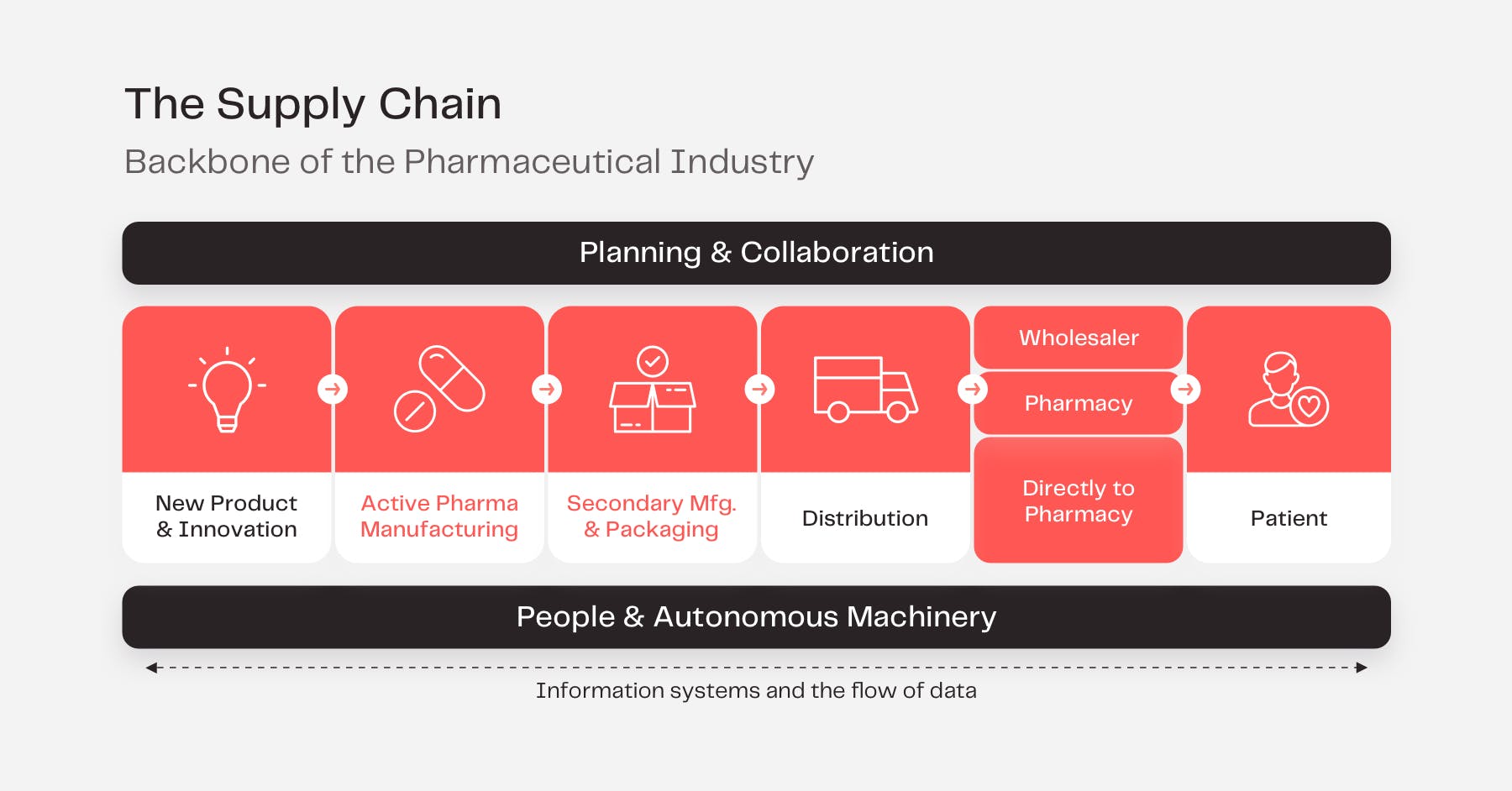
General industry observations indicate that pharma supply chains are becoming more fragmented as the world becomes increasingly complex. To add to this, manufacturers must factor in a number of supply chain conditions during the production process:
- Stock shortages
- Product damage
- Supply chain agility
- Temperature control
- Human resource dependency
- Sanitation and hygiene standards
- Increasing costs of manufacturing and transport
- Adherence to, and compliance with, worldwide regulations
- Pressure from patients (product, timeliness, quality, price, etc.)
- Lack of transparency, mistrust, and an unwillingness to share data
Non-sustainable inputs(49%), the lack of visibility on supplier risks(25%), concentrated production(23%), demand variability(23%), and long lead times(23%) are among the most critical conditions making pharma companies vulnerable to supply chain disruptions.
Providing a solution to these challenges, new supply chain technology is unlocking immense opportunities for the industry. IoT, artificial intelligence, and machine learning enable automation capabilities across the entire production line, as well as the ability to gather, sort, and analyze data. Integrating digital technologies into the supply chain is expected to save hundreds of worker hours – for example with the elimination of 80% of manual documentation work – since these systems can automatically generate performance reports or reports required for site inspections by regulatory authorities. This technology will also solve one of the biggest challenges in pharma: visibility across the supply chain. Greater transparency will help the industry improve production efficiency, data security, product quality, and ultimately boost profitability for pharmaceutical companies that invest in robust supply chain technologies.
With industry reports making the extensive benefits of digital supply chains abundantly clear, pharma executives are aiming to integrate technology in supply chain management for two reasons: (1) 97% of executives agreed that digital technology will enhance supply chain capabilities to get closer to patients; and (2) 73% of executives believe that the role of pharma supply chains will become a new type of customer service provider.
The pharmaceutical industry is undergoing a shift toward continuous manufacturing processes, with many businesses experiencing increased efficiency and cost savings as a result. Continuous manufacturing has moved out of pre-clinical and clinical manufacturing to include full-scale production both in drug substance manufacturing and product manufacturing. These types of manufacturing plants often require smaller facilities that focus on more flexible production processes with regular small-scale individualized batch outputs.
The benefits of this include:
- A decrease in production costs of 15% - 30%
- An increased overall equipment efficiency (OEE) of 75%
- A 60% - 80% reduction in end-to-end batch lead time
- Significant reductions in inventory and utility costs.
Pharma companies are recognizing that it’s no longer feasible to be independent players in the market. Companies are collaborating with ecosystem partners both vertically and horizontally to extend their supply chain network, increase resiliency, and integrate their processes and systems. This illustrates a shift from company-thinking to network-thinking and highlights the transition to deploying strategies designed to monitor, respond, and manage the complexities that are present in today’s supply chain systems.
Although pharma has typically been a risk-averse industry, logistics executives rank technology as the most important factor to improve supply chain capabilities. Despite a previous lack of buy-in from corporate decision-makers to invest in new technologies, barriers to technology adoption will continue to fall, and digital strategies that form the framework of pharma 4.0 will become the new standard.
Digital Solutions: The Emergence of Pharma 4.0
Pharma 4.0 can be thought of as the convergence of people, physical systems, and data in the context of pharmaceutical manufacturing to increase quality, productivity, and profit using advanced data analytics.
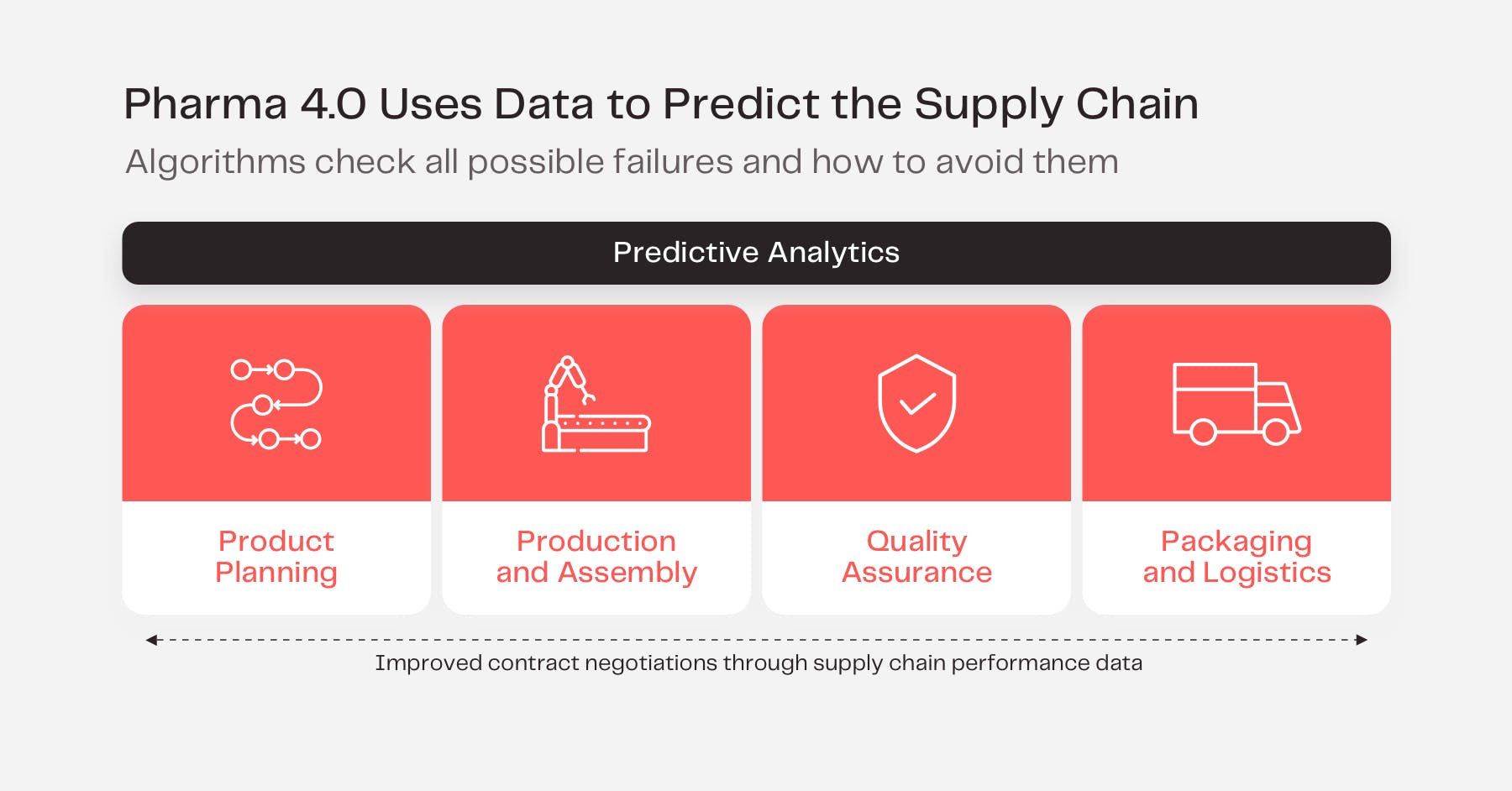
The promise of pharma 4.0 lies in its ability to unlock higher levels of efficiency and quality in the manufacturing process. Data integrity is another area where pharma 4.0 can contribute the most.
Pharma 4.0: Three Critical Drivers
A strategy to remain competitive
- A strategy to remain competitive
- Real-time monitoring and reporting
- The rapid development of new and improved products
1. A strategy to remain competitive
In today’s competitive market, pharmaceutical companies are quickly realizing that improving supply chain performance is critical to maintaining a competitive edge. Competitive advantage in pharma is no longer only based on the principle of economies of scale in production, but instead focuses much more on how IoT can improve the supply chain.
What makes this possible?
- Companies are transitioning from CapEx to OpEx to avoid large upfront investments for equipment spending
- IoT creates nearly no deviation during production (at least no deviation relevant to quality standards) via PAT (process analytical technology)
- IoT enables agile production:
- Production on-demand/ batch flexibilization (made to order)
- Shorter throughput times
- Fast and flexible scale-up
- Output and demand forecasting capabilities
2. Real-time monitoring and reporting
Pharma manufacturers are beginning to invest in digital technologies that leverage big data collected from smart sensors to improve process efficiency.
What makes this possible?
- This is made possible by retrofitting existing systems with digital components. This reduces costs by avoiding the integration of entirely new digital systems.
- Manufacturers are increasing the number of smart sensors across the supply chain from production to distribution to gather information at every stage of the value chain (product quality, location, defect tracking, etc.). Forecasts suggest that by 2027, the global track and trace solutions market will increase to around $6 billion.
- Manufacturers use big data to maintain and improve product quality made possible via PAT. This real-time data is used to initiate countermeasures early on if any production deviation occurs.
3. The rapid development of new and improved products
Significant losses often occur during the manufacturing process from the mismanagement of resources. Pharmaceutical manufacturers are deploying digital systems to have continuous oversight of each step in the production process.
What makes this possible?
- Manufacturers are deploying automated technology to scale up efficiently and sustainably (reducing byproducts and waste during production processes)
- Manufacturers use data analysis to find the best-operating conditions
- Manufacturers standardize procedures supported by big data
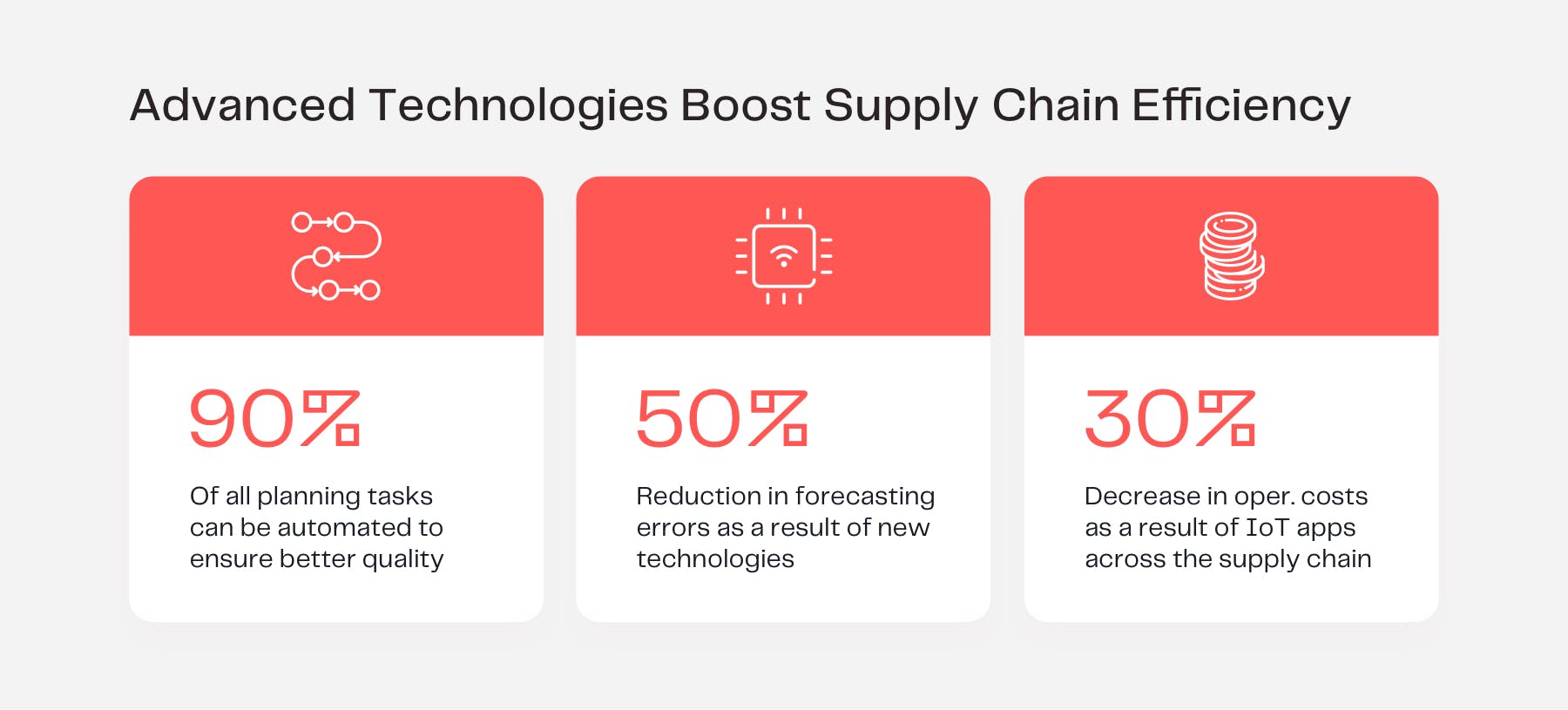
Benchmarking Current Pharma Use Cases
Pharma 4.0 promises the enhanced interpretation of data collected throughout a product’s lifecycle. Managing the movement of information is just as important as the movement of products. With advances in AI and ML, digital interfaces are able to autonomously discover connections within large data sets and take these findings to continuously optimize each stage of the supply chain. Although many applications of supply chain solutions already exist, below is an overview of 13 use cases already creating value in pharma today.
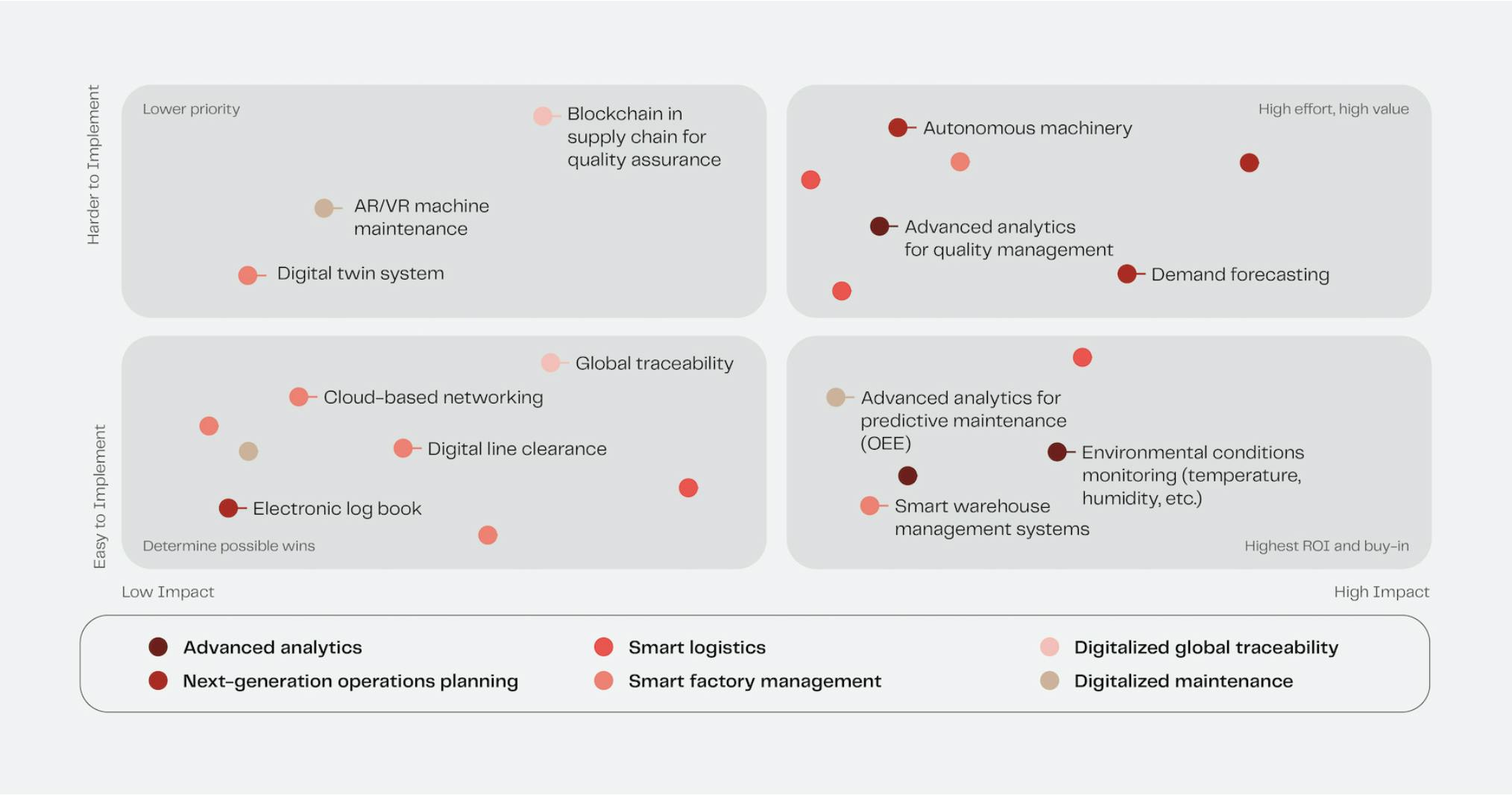
Future Use Cases: Three Prime Opportunities
Digital technologies are redefining how pharma is conducting business. Real-time monitoring and traceability are rated as the most important strategic priority for life sciences logistics leaders when implementing new technology with 15% of respondents highlighting this as a high priority in biopharma cold chain logistics.
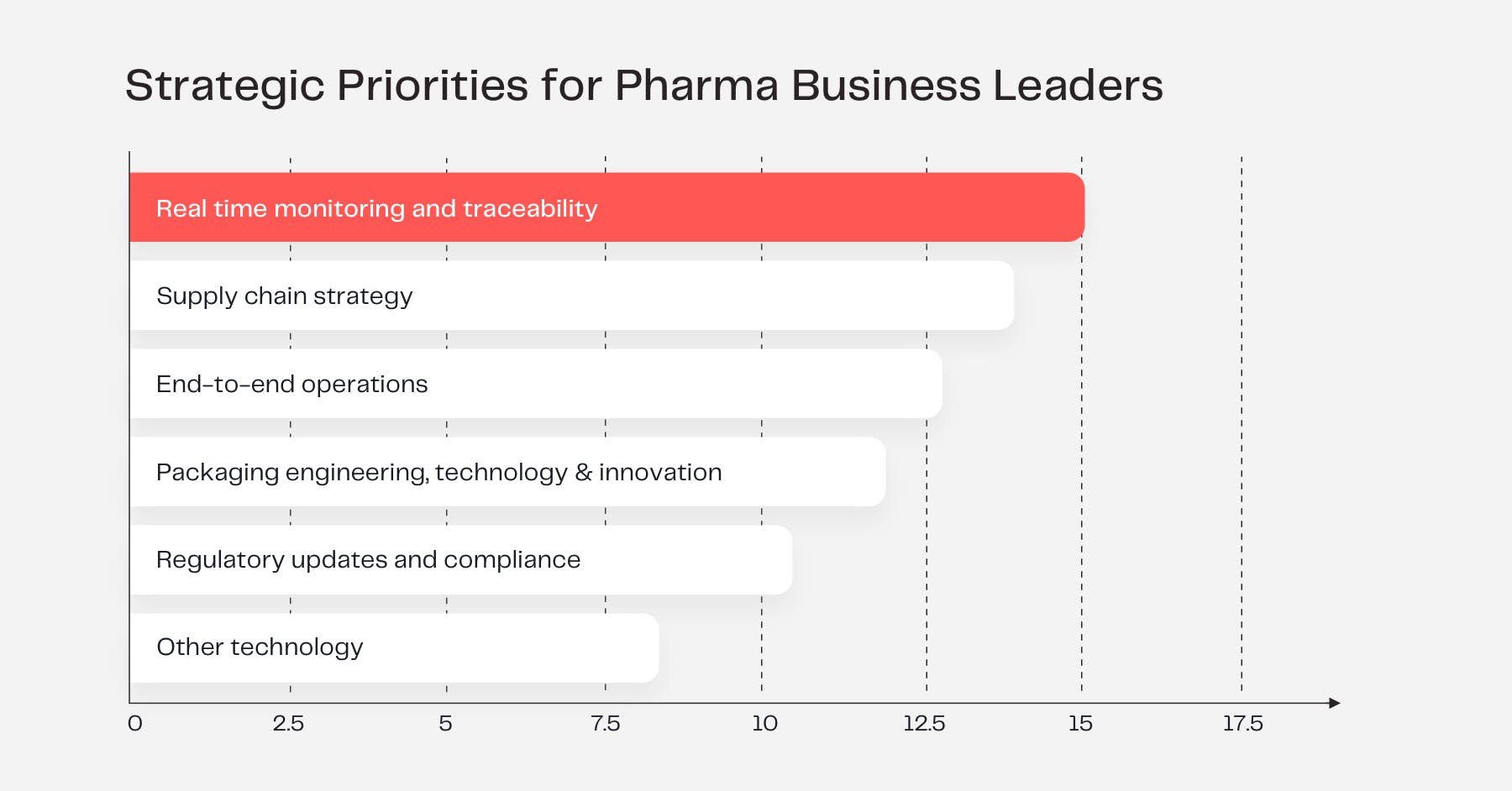
While there is unlocked potential in the adoption of new technologies, implementation can be challenging. Each use case is analyzed on current opportunities, existing challenges, and potential solutions.
The use cases:
- IoT to improve transparency across the pharma supply chain
- IoT to minimize waste management across the supply chain
- IoT solutions for medical adherence (not directly supply chain-related)
1. IoT to improve the transparency of pharma supply chain operations
Opportunity: Cold chain becomes innovation hotspot
- Temperature-controlled logistics form only 20% of the total pharmaceutical logistics market, however, the amount of products that require special temperature treatment is rising fast.
- Each year, the pharma industry loses between $2.5 - $12.5 billion as a result of temperature control irregularities during transit. Half of these losses occur while shipments are in the hands of airlines.
- The cost of replacing products could cost manufacturers up to $35 billion in damages, highlighting the urgent need for smart environmental sensors.
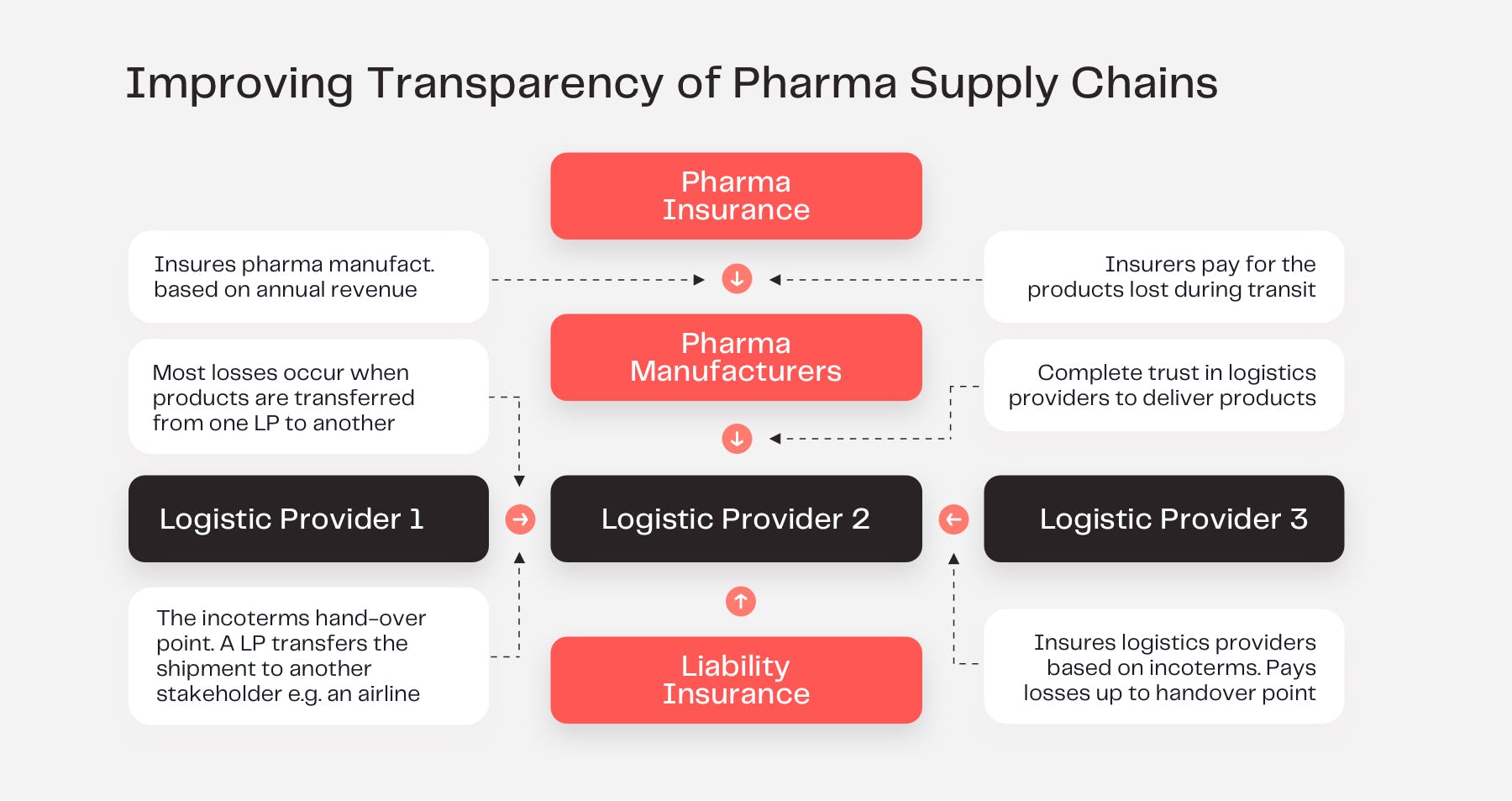
Challenges
- Pharma manufacturers and logistics providers often overlook investing in new solutions as it’s assumed that losses will be compensated by insurance companies.
- A lack of corporate buy-in or understanding surrounding disruptive technologies – especially blockchain technology – prevents companies from exploring these solutions. Negative perceptions around the scale of equipment spending also contribute to this.
Possible Solution
Recent findings forecast a 12.7% annual increase in cold-chain pharmaceuticals, which puts an additional strain on cold chain logistics. As cold chains and temperature control become more important, IoT can offer a solution to save costs, and improve the quality, and efficiency of its logistics activities. Cold chain products often have a large proportion of high-value active ingredients with shorter shelf lives and strict temperature requirements. IoT-based solutions can help pharma manufacturers remotely monitor cold chain environments in real-time with embedded sensors on tracking equipment. Environmental sensors inside product packages/pallets in transport containers continually track the temperature of drugs and are often programmed with start-or-shut-down mechanisms. Sensors will automatically signal alerts via a mobile app if storage moves outside a specified temperature range – whether this occurs during scheduled removal from a refrigerated environment to a shipping container, or due to a cold chain malfunction.
2. IoT to minimize waste management across the supply chain
Opportunity: Opting for sustainable ethics in pharma
- Globally, around 100,000 tons of synthetic chemicals are produced each year. From this, only a fraction of these chemicals are being utilized while the rest is left unused or eventually expires, resulting in large volumes of pharmaceutical, and potentially hazardous, waste.
- The value of unused medications in the US alone is estimated to be over $ 1 billion per year. Similar observations have been noted in other developed countries - like Australia - where the economic value of pharmaceutical waste per patient sums up to $1280 each year.
Challenges
- There is a lack of infrastructure that enables incentives for industry stakeholders to improve efficiency and reduce wastage.
- There is a lack of transparency around what happens to expired medication.
Possible Solution
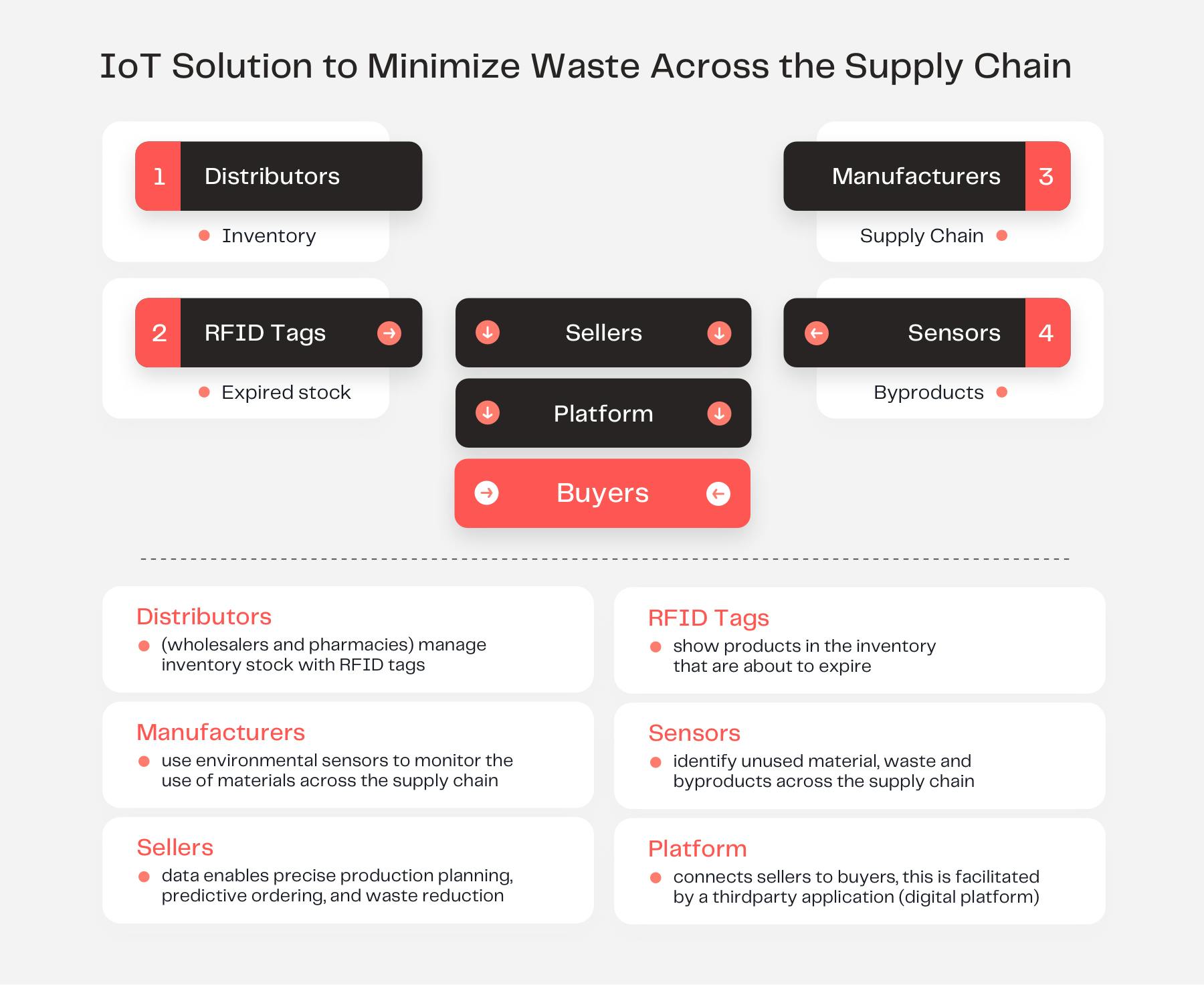
3. IoT solutions for medical adherence
Although this use case does not specifically center around the manufacturing process, it should already be a consideration at the manufacturing stage to extend the impact of their value chain. The choice between profits and patients should not be mutually exclusive.
Opportunity: Developing a patient-centric supply chain
- On average, 50% of prescription medication is not taken as prescribed to patients.
- Non-adherence has a negative impact on patient wellbeing and represents a major barrier to realizing the benefits of evidence-based therapies. The economic impact of non-adherence on scarce healthcare resources is also significant.
- The advancement in IoT and data analytics has driven numerous efforts in developing sensor-based solutions for drug adherence.
Challenges
- Despite many efforts in developing medication management technologies, the challenge of reducing non-adherence is still unmet.
- Currently, most solutions only offer a fixed-time reminder. No personalized adherence interventions exist.
- There is a lack of accurate data to signal actual medication intake.
Possible Solution
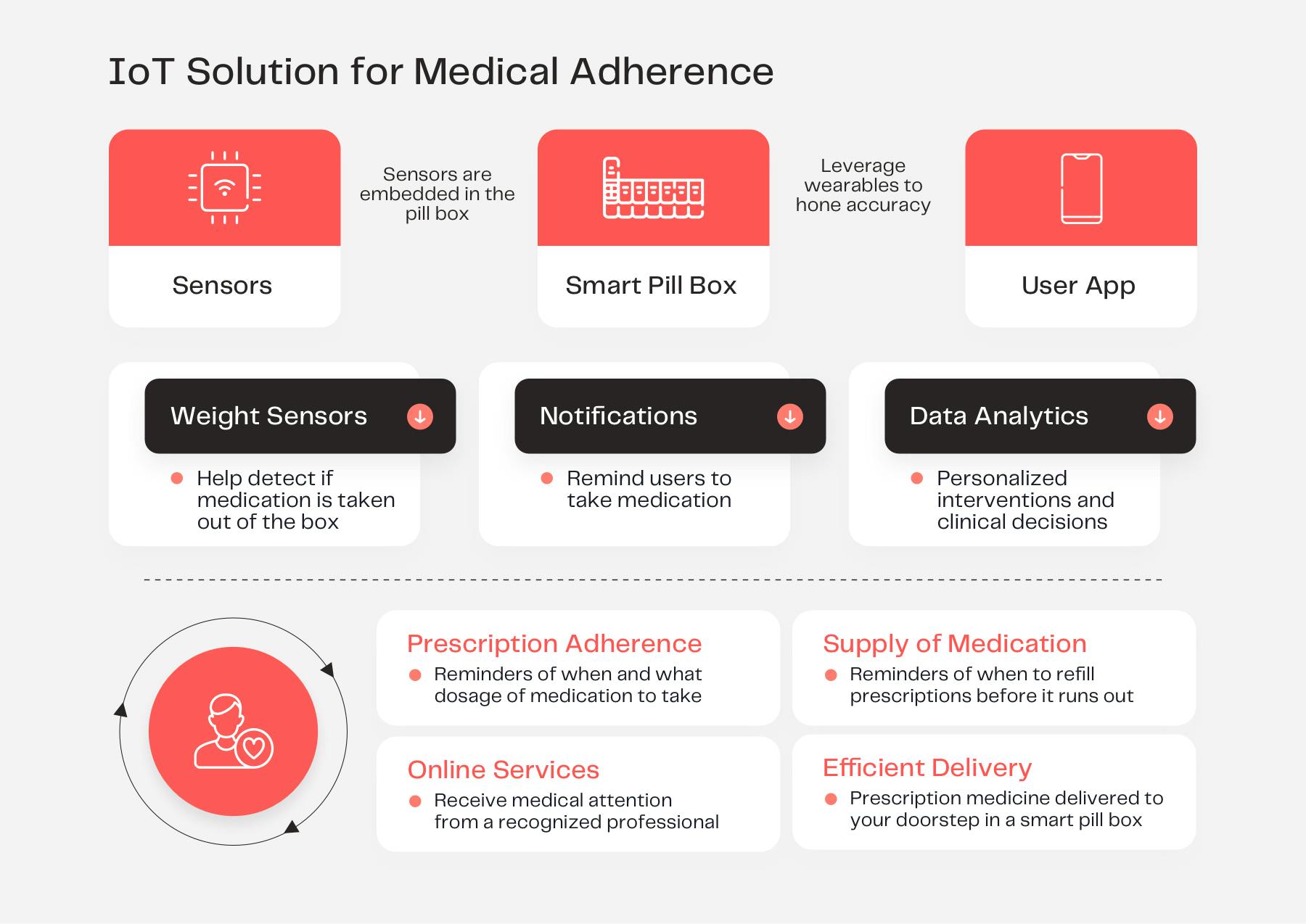
End-to-end supply chain visibility involves going beyond the application of new technologies. It involves breaking down silos that occur across organizations, entire networks, and patients. Data must be collected from both internal (suppliers, manufacturers, distributors) and external (patients) sources.
Don’t Rush a Revolution - Prioritize a Steady Evolution
In pharma manufacturing, digital transformation is often positioned as a technological problem, but it need not be. For many manufacturers in highly regulated industries, sacrificing continuous improvement for compliance is the cost of doing business, and the same goes for pharma.
Technology writer, Alasdair Gilchrist, speaks of ‘the power of 1%’, which refers to the idea that the industry only needs to decrease operational costs by just 1% through the application of Industry 4.0 principles to realize significant savings. He gives the following examples:
- If the aviation industry could save 1% of fuel costs per year, it would save $30 billion.
- If a gas-fired power station could save 1% on gas per year, it would save $66 billion.
- If the oil and gas industry could reduce capital spending on equipment by 1% per year, it would save $90 billion.
“The pharmaceutical supply chain needs to adopt the ‘power of the 1%’ mindset and use IoT as a way to a solution.”
Pharmaceutical manufacturers can realize significant gains by finding small opportunities for digitization and starting there. With IoT implementations in pharma, improvements don’t need to be large, costly endeavors.
The Way to an Industry-Wide Solution: Technology as an Ally
With the introduction of digital technology to automate simple manual processes, the goal is to find repetitive tasks that would be better performed by computers, robotics, or autonomous machinery. Pharmaceutical manufacturing is shifting toward faster development cycles, higher product mixes, and increased digitization. Pharma companies wanting to implement IoT into the value chain, there are five stages of digital maturity that outline a path that all manufacturers can follow.
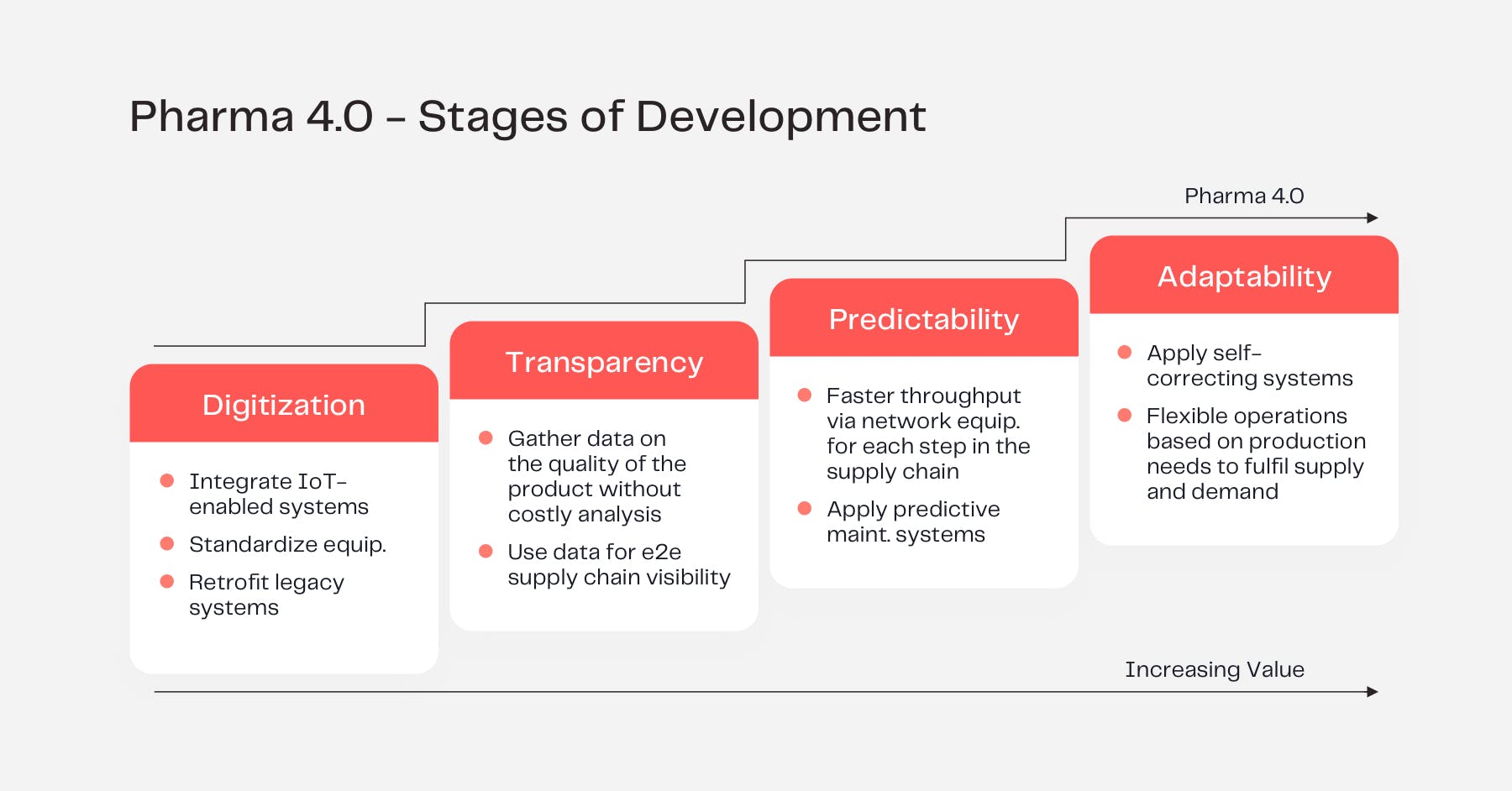
Pharma manufacturers that succeed in this approach will be those that find digital solutions to increase operational efficiency and agility across the supply chain. Today, more technologies and tools are available than ever before to help pharma manufacturers shape a world where patient needs are prioritized and as a result, profits will inevitably follow.