Promoting Environmental Sustainability: The Imperative of Resource-Efficient Manufacturing
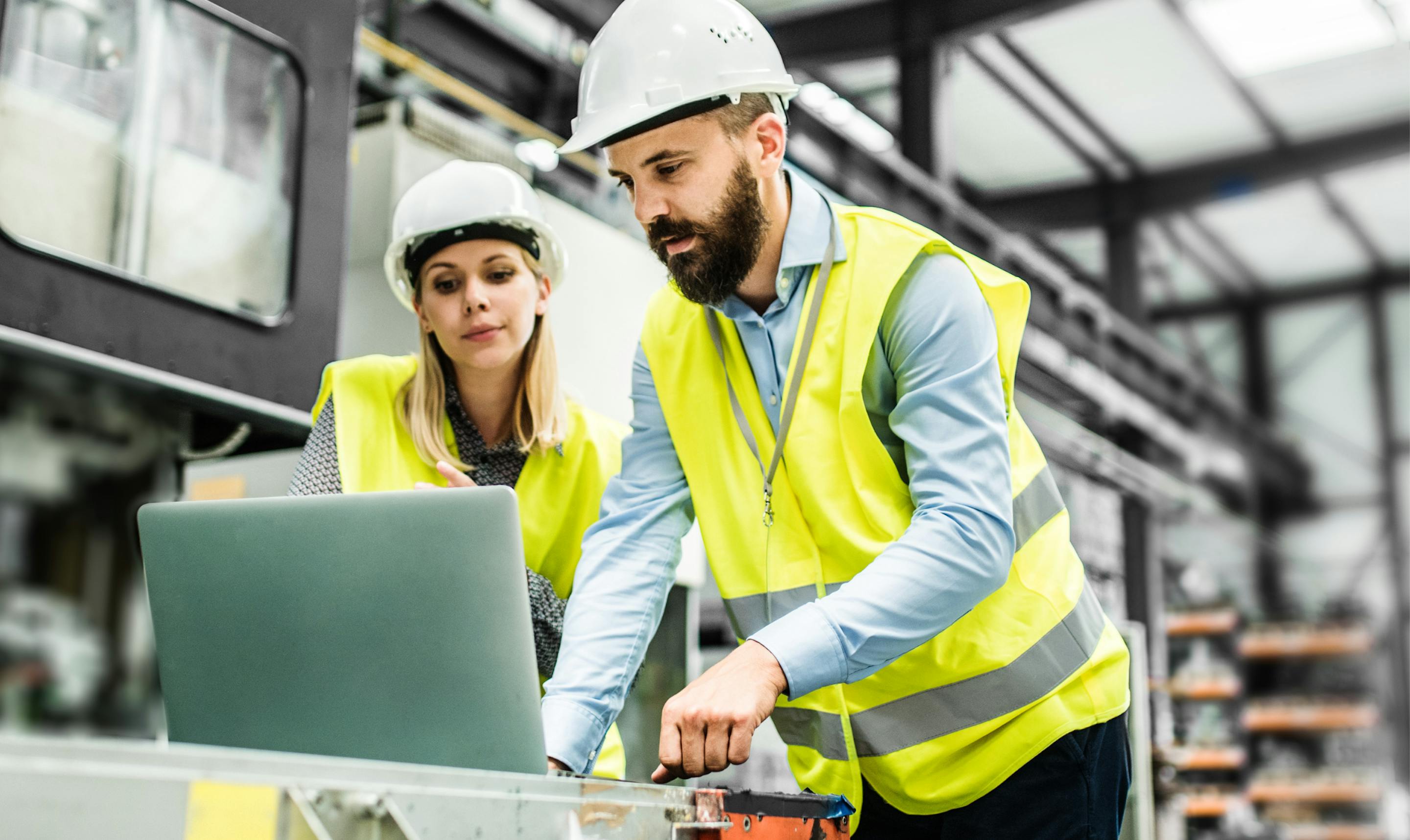
Traditional manufacturing methods have their limitations, from high energy consumption and carbon emissions to inefficient use of raw materials and limited recycling infrastructure. But the days of reckless resource consumption in manufacturing are over. The world is demanding sustainable and eco-friendly products. Consumers are more conscious than ever about the environmental impact of the products they purchase. Manufacturing companies need to answer this call of sustainability by taking proactive steps to reduce their environmental footprint. Technologies like the Internet of Things (IoT) and Artificial Intelligence (AI) offer the tools necessary to make this transition. In this article, we're diving deep into the world of resource-efficient manufacturing through technology to inspire and to show you the incredible opportunities and the urgent necessity of transforming the manufacturing landscape.
Shaping a Greener World: Why Manufacturing Companies Must Be at the Forefront
Resource-efficient manufacturing is not just a choice; it's an essential component of a future-proof and sustainable economy. This groundbreaking concept enables companies to keep pace with the challenges of the 21st century while making a positive contribution to the environment.
But why? These are some aspects of making it a crucial imperative for the manufacturing sector:
Promoting Environmental Sustainability
Conventional manufacturing practices often result in the excessive use of resources, which in turn leads to environmental degradation. By adopting resource-efficient processes, we can effectively reduce our carbon footprint, minimize greenhouse gas emissions, and safeguard natural ecosystems. These efforts are crucial for creating a more sustainable planet.
Responding to Consumer Demands
As described above, today’s consumers are increasingly environmentally conscious and favor products that are produced sustainably. Manufacturers that adopt resource-efficient practices not only meet these consumer preferences but also gain a competitive edge and foster greater brand loyalty.
Addressing Resource Scarcity
With the increasing global population, there is a growing demand for finite resources such as water, energy, and raw materials. Implementing resource-efficient manufacturing practices ensures the responsible and careful use of these valuable resources, mitigating the risk of scarcity and potential conflicts over access.
Cost Efficiency
Making efficient use of resources results in significant cost savings for manufacturers. By minimizing waste and optimizing processes, companies can reduce their production expenses, improve their overall profitability, and gain a competitive edge in the market.
Meeting Regulatory Requirements
Environmental regulations and standards are becoming more rigorous. Implementing resource-efficient manufacturing practices helps companies ensure compliance with these regulations, avoiding fines and legal complications, while also enhancing their corporate image.
Encouraging Innovation and Technological Progress
The pursuit of resource efficiency often sparks innovation. Manufacturers striving to minimize waste and enhance efficiency frequently develop and adopt new technologies and processes, thereby fostering advancements throughout the industry and remaining relevant in rapidly evolving markets.
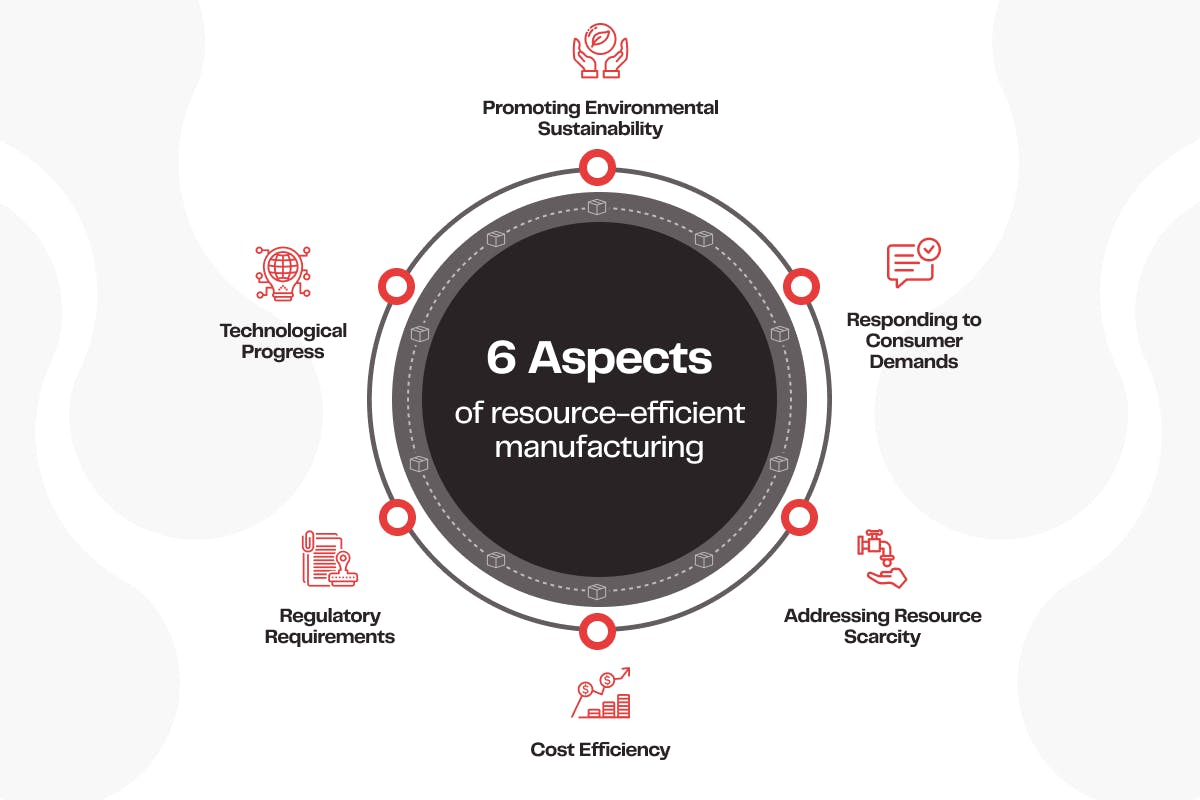
Unleashing the Power of Resource Efficient Manufacturing
But how can companies achieve resource-efficient production? While saving energy is an important aspect, it alone is not sufficient, especially since it is already being practiced to some extent. This is where new technologies play a crucial role. The utilization of the Internet of Things (IoT) and Artificial Intelligence (AI) enables better control and monitoring of various aspects of the production process, consistently identifying opportunities for more efficient resource utilization.
IoT sensors, for example, transform machines into intelligent entities. It allows for the seamless integration of physical devices, sensors, and machinery with digital systems, enabling the exchange of data and facilitating intelligent decision-making.
AI can analyze vast amounts of data in real-time to optimize the allocation of resources such as energy, materials, and labor. The systems can continuously learn and adapt. The combination of both technologies provides actionable insights from data, helping companies make informed decisions about resource allocation, process improvements, and overall production strategies.
The integration of new technologies into production thus presents a promising future perspective. Resource-efficient production not only facilitates a more effective use of resources but also enhances operational efficiency. It is high time to embrace these advanced technologies and contribute to sustainable and environmentally friendly production.
Now, let us journey into the core of resource-efficient manufacturing and explore the vast array of possibilities that IoT and AI already bring forth. The first application may be obvious – but you might be surprised by the others.
1 Optimized Energy Management
Industrial processing and manufacturing facilities tend to be the largest consumers. Consequently, energy costs represent a substantial portion of operational expenses in manufacturing. Through optimized energy management, these costs can be reduced, thereby enhancing the overall profitability of the production process.
But optimizing the energy management not only decreases costs – it also minimizes carbon emissions and supports environmentally friendly production practices. Recognizing that energy is a finite resource, conserving it becomes crucial for long-term sustainability. By utilizing energy efficiently, we ensure that future generations have access to this valuable resource.
Moreover, a stable and efficient energy supply is vital for sustaining production processes and preventing downtime. Effective energy management ensures the smooth operation of production lines, minimizing disruptions.
Technologies such as A1 Digital Energy Insight for example provide solutions by measuring the energy consumption of individual devices, machines, and plants across various locations. This enables manufacturers to monitor their power consumption in real time and analyze their data to identify optimization opportunities. By utilizing the energy monitoring solution, manufacturers can pinpoint their largest energy consumers, detect anomalies, and measure the impact of their energy-saving initiatives.
2 Inventory Management
Efficient management of inventory revolutionizes resource-efficient manufacturing by utilizing IoT sensors and AI for real-time inventory data. This enables manufacturers to fine-tune stock levels and reduce overproduction. This precise allocation of resources not only brings cost savings but also benefits the environment. Two key aspects are particularly noteworthy:
Waste Reduction through Inventory Tracking
Innovations like Swift Count, an AI-powered inventory management system developed for manufacturing, utilize IoT sensors and computer vision technology to monitor inventory levels in real-time. By providing immediate insights, this approach enables manufacturers to receive and utilize materials and components precisely when they are needed for production. Consequently, the need for large stockpiles of raw materials or finished products is reduced, minimizing the risk of waste. Moreover, it helps prevent overproduction and reduces the chances of excess inventory becoming obsolete.
Streamlining Supply Chains with Real-time Data
Real-time data from IoT sensors plays a vital role in streamlining supply chain processes by optimizing inventory levels. This allows businesses to minimize excess stock while meeting demand, resulting in improved cash flow and reduced carrying costs.
The concept of a sustainable supply chain and logistics has gained immense significance. Discover more about the pivotal role that Internet of Things (IoT) technologies play in revolutionizing this sector.
3. Production Optimization
IoT-driven production optimization means being nimble and responsive. By adopting this technology, manufacturers can gather real-time data on various aspects of the production line. This collected data is then analyzed to identify any weaknesses and implement strategies aimed at enhancing efficiency and minimizing environmental impact. The result: manufacturers can adapt to changes swiftly. It's manufacturing at its most efficient and sustainable.
US start-up Neurala for example reports a use case at IHI Logistics & Machinery with a focus on managing food packaging information and improving logistics processes. Here, the vision AI software will be deployed to increase the effectiveness of optical character recognition (OCR) reading for process optimization and waste reduction.
Another notable example is SightMachine, an advanced analytics platform that leverages machine learning and IoT sensors to optimize manufacturing processes. By seamlessly integrating multiple data sources and elements, SightMachine continuously monitors the states of individual tags as well as the overall machine. The platform features a robust real-time data streaming pipeline that handles out-of-order data, late-arriving data, and missing data. With powerful visualization capabilities and advanced analytics, users can conduct in-depth analyses of individual machines or evaluate an entire fleet of machines.
4. Predictive Maintenance
Unplanned downtime poses a significant threat to manufacturing operations, resulting in substantial losses. Industrial manufacturers lose approximately $50 billion annually due to machine failures.
These machine failures and quality deviations are often caused by operational blind spots within plant operations. However, IoT sensors and AI applications have the ability to detect and uncover these blind spots in real-time. By providing actionable insights, operations and maintenance teams can proactively address these events before they have a negative impact on operations. Making predictive decisions to perform condition-based maintenance minimizes downtime in production. This reduces resources wasted on emergency repairs.
The Israeli company Augury calls this process of predictive maintenance “Listening to Machine Health”. Their platform uses vibration and ultrasonic sensors to monitor equipment and identify potential issues before they cause downtime or damage.
Another advantage of predictive maintenance is its ability to improve equipment lifespan. By proactively addressing maintenance issues, replacing worn-out components, and ensuring proper calibration, businesses can maximize the longevity of their assets. This approach not only reduces the need for premature equipment replacements but also lowers overall operational costs associated with acquiring new machinery.
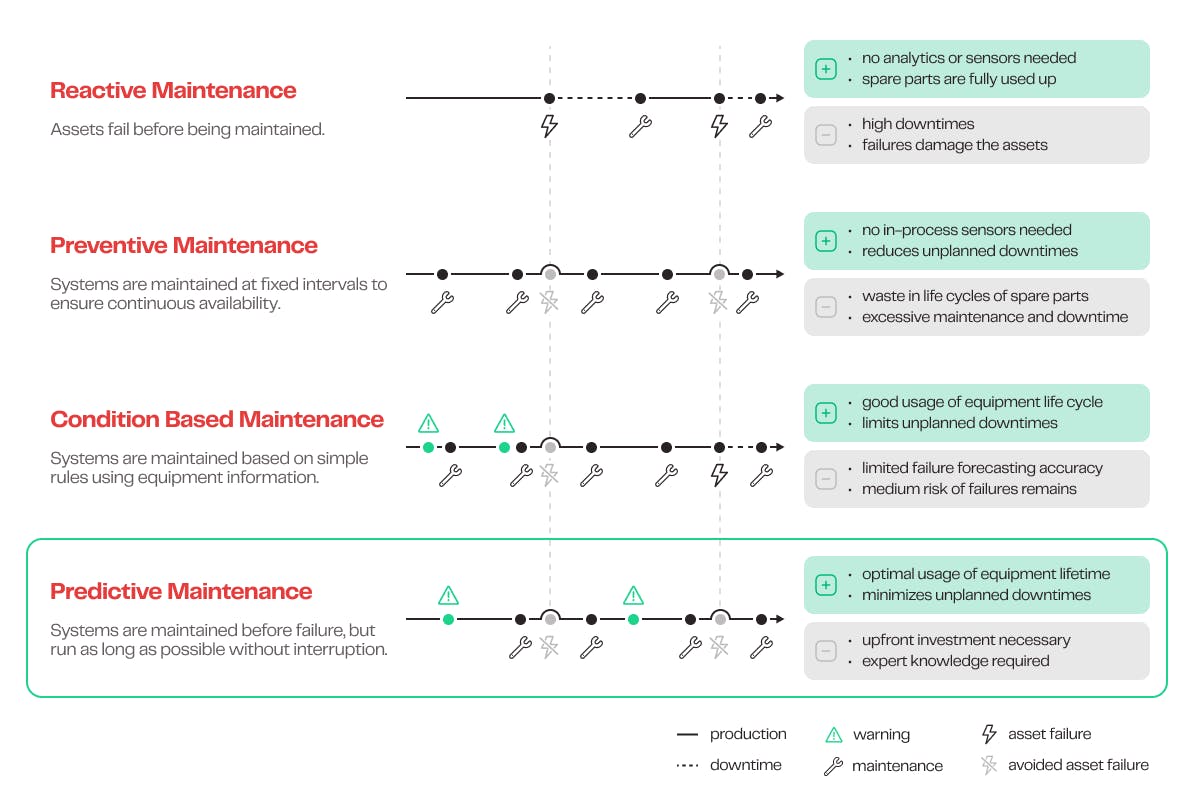
5. Construction Material Optimization
The efficient use of raw material as well as the recycling and reuse of waste is an important topic when it comes to resource-efficient manufacturing. Let’s take the example of the construction industry.
Concrete, the most extensively used building material globally, heavily relies on a critical resource - suitable sand, which is currently facing scarcity. Moreover, concrete production is far from environmentally friendly. In fact, it is estimated that concrete contributes up to 8% of the world’s man-made carbon dioxide emissions, making it one of the primary sources of such emissions.
NBT's portfolio venture ConcR has developed smart IoT sensors for digital concrete monitoring. By using the sensors, construction companies not only save time and money, but have also proven to save precious material.
Other start-ups are tackling this challenge by focusing on improved recycling of construction waste. On an average construction site, it is estimated that the waste generated can amount to approximately 30% of the total weight of building materials delivered.Studies conducted in the US have revealed that construction and demolition debris accounts for approximately 23% of the national waste stream. It is projected that annual construction waste worldwide will reach 2.2 billion tons by 2025.
At present, 75% of construction and demolition waste in the EU is being landfilled, although over 80% recycling rates have been exceptionally achieved in countries such as Germany and the Netherlands. AMP Robotics has developed an AI-powered robotic waste sorting systems, using sensors to detect and sort different types of waste materials. The solution helps improving the recycling process and reducing waste sent to landfills.
It is Time to Contribute to Sustainable and Environmentally Friendly Production by Resource Efficient Manufacturing
At NBT, we're on a mission to empower visionaries and founders to challenge the status quo. Resource-efficient manufacturing through IoT and AI is not just a buzzword; it's a movement. It's a movement that NBT is proud to champion. We believe in a future where innovation and sustainability walk hand in hand.
As you embark on your journey into this exciting world, remember that you're not just improving your business; you're helping shape a better, more liveable future for all of us.
So, if you're such a founder looking to challenge the status quo and create impactful tech startups for a livable future: Explore NBT's pioneering venture-building approach and extensive thought leadership.
Let's tackle the chances and the necessity of resource efficient manufacturing and pave the way towards a greener, more sustainable tomorrow. Get ready to revolutionize the manufacturing industry – together, we can make a difference!