12 IIoT Use Cases Unlocking True Business Potential
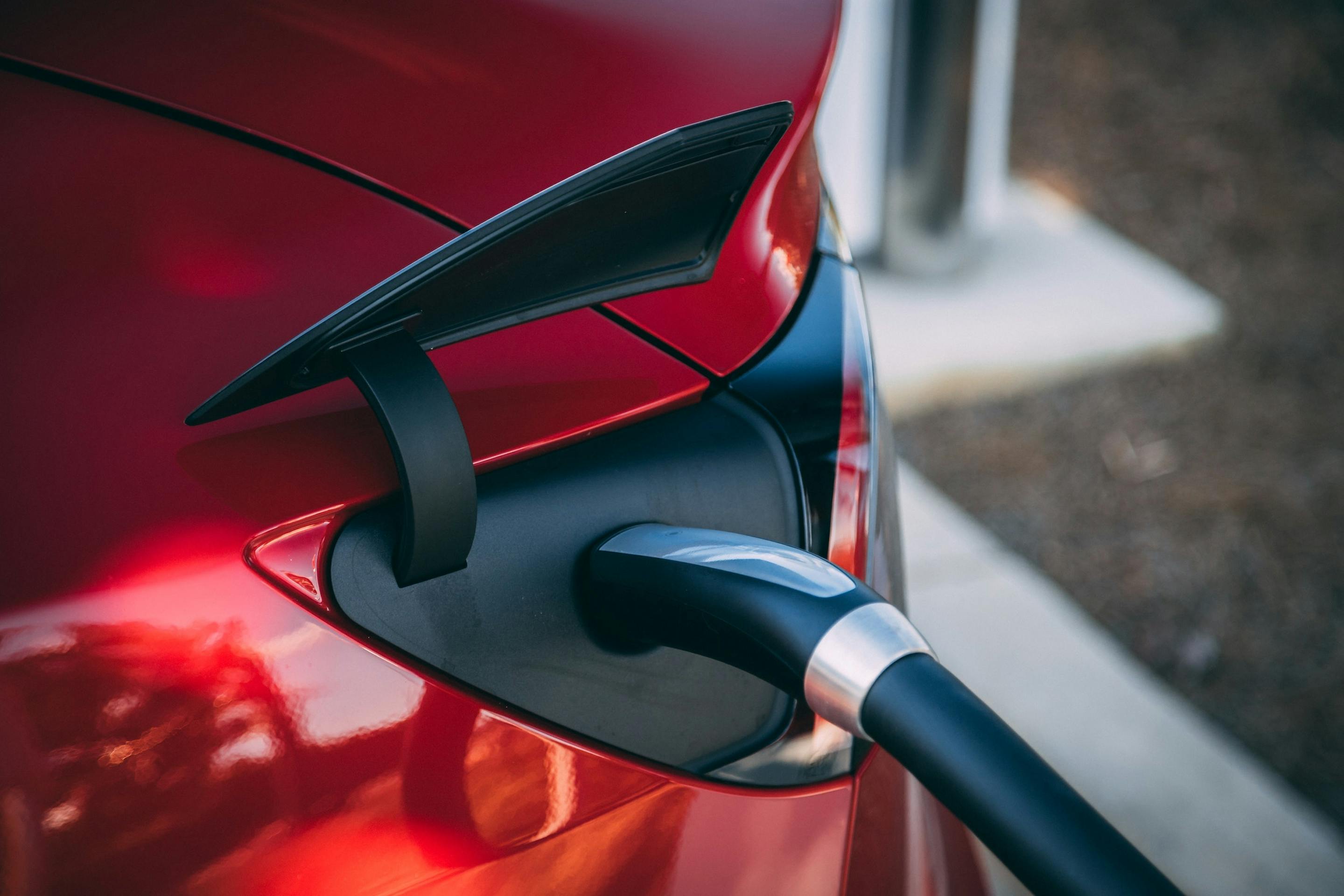
In the business environment where competitive pressure continues to rise, organizations are looking toward IIoT as a solution to revolutionize the manufacturing industry through data intelligence and process optimization.
Although IoT and Industrial IoT share common technologies (sensors, connectivity, and data analytics), the difference comes in their general usages. In contrast with IoT, which mostly centers around human interaction with smart devices, IIoT focuses on disruptive technologies and intelligent machinery within the manufacturing and industrial sectors.
Disruptive technologies such as machine-to-machine (M2M) communication, edge computing, distributed ledger technology (DLT), robotics and artificial intelligence (AI) are bringing new levels of automation and actionable intelligence that allow for comprehensive data to be gathered, analyzed and shared. From a business perspective, this is fundamentally changing the way organizations operate. By combining relevant technologies with newly available data, industrial equipment and processes are being optimized to enhance productivity, profitability, and reliability in ways previously unimagined. According to Microsoft’s IoT Signals, 94% of businesses state that they will be implementing IoT by the end of 2021.
IIoT is increasingly gaining a foothold in the market as more organizations are realizing the exponential value and return on investment (ROI) of connected machinery. Although IIoT is in its nascent phase, it is showing immense potential as a solution to some of the manufacturing industry’s most challenging problems. Advances in connected sensors, communication mechanisms, data management, and robotics are opening up entirely new value streams through the application of smart, accurate, and automated manufacturing processes. Forecasts predict that the global industrial IoT market is set to reach $949.42 billion in 2025.
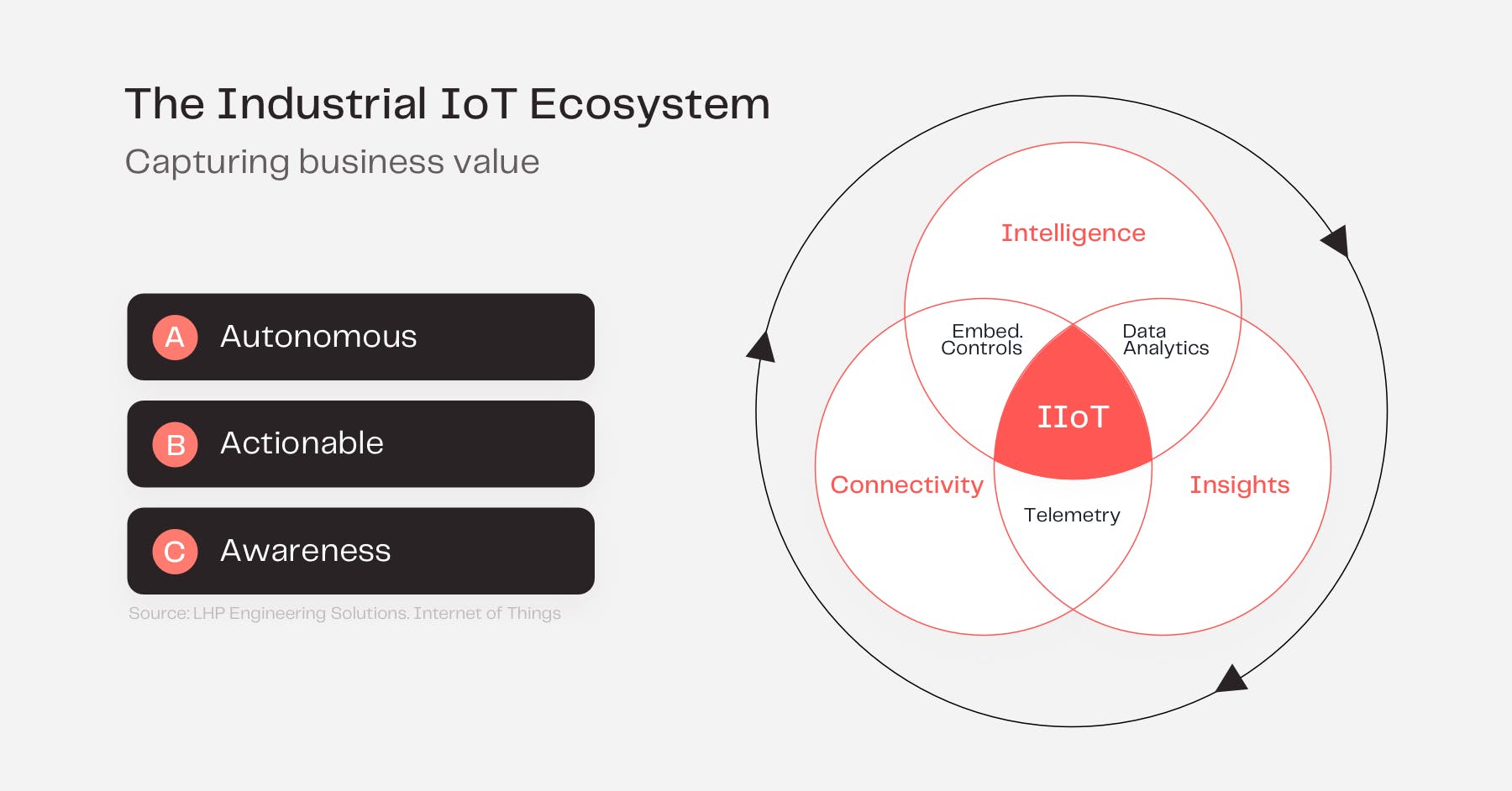
Within the IIoT ecosystem, there are four key findings:
1. IIoT systems execute awareness and autonomy that delivers actionable insights for manufacturers and business owners
2. IIoT provides a wide breadth of tools and processes (embedded controls data analytics and telemetry) to bridge the gap between big data and decision making
3. IIoT forms a modern development and productivity enabler for traditional Manufacturing Execution Systems (MES)
4. Manufacturers leverage IIoT’s ecosystem trifecta of intelligence, connectivity, and insights to establish low-cost, quick-to-implement and scalable solutions
IIoT Value Drivers for Improving Business
Successful applications of IoT in business are the building blocks of digital transformation. However, clearly defining a business case, selecting primary objectives, and prioritizing each one to drive real business impact, is a critical first step to achieving long-term success.
As one of the most data-prolific industries, manufacturers leverage IIoT as a means of achieving targeted goals that save time, boost profitability, and enable businesses to leap ahead of competitors.
Although many IIoT projects are still in the proof-of-concept (PoC) phase, IIoT is already demonstrating its prosperity and versatility with live deployments in various organizations, proving what’s already possible with different use cases across industry domains. As asset-intensive industries continue to redesign their business operations to incorporate IIoT, here are the top 12 use cases accelerating business efficiency and success:
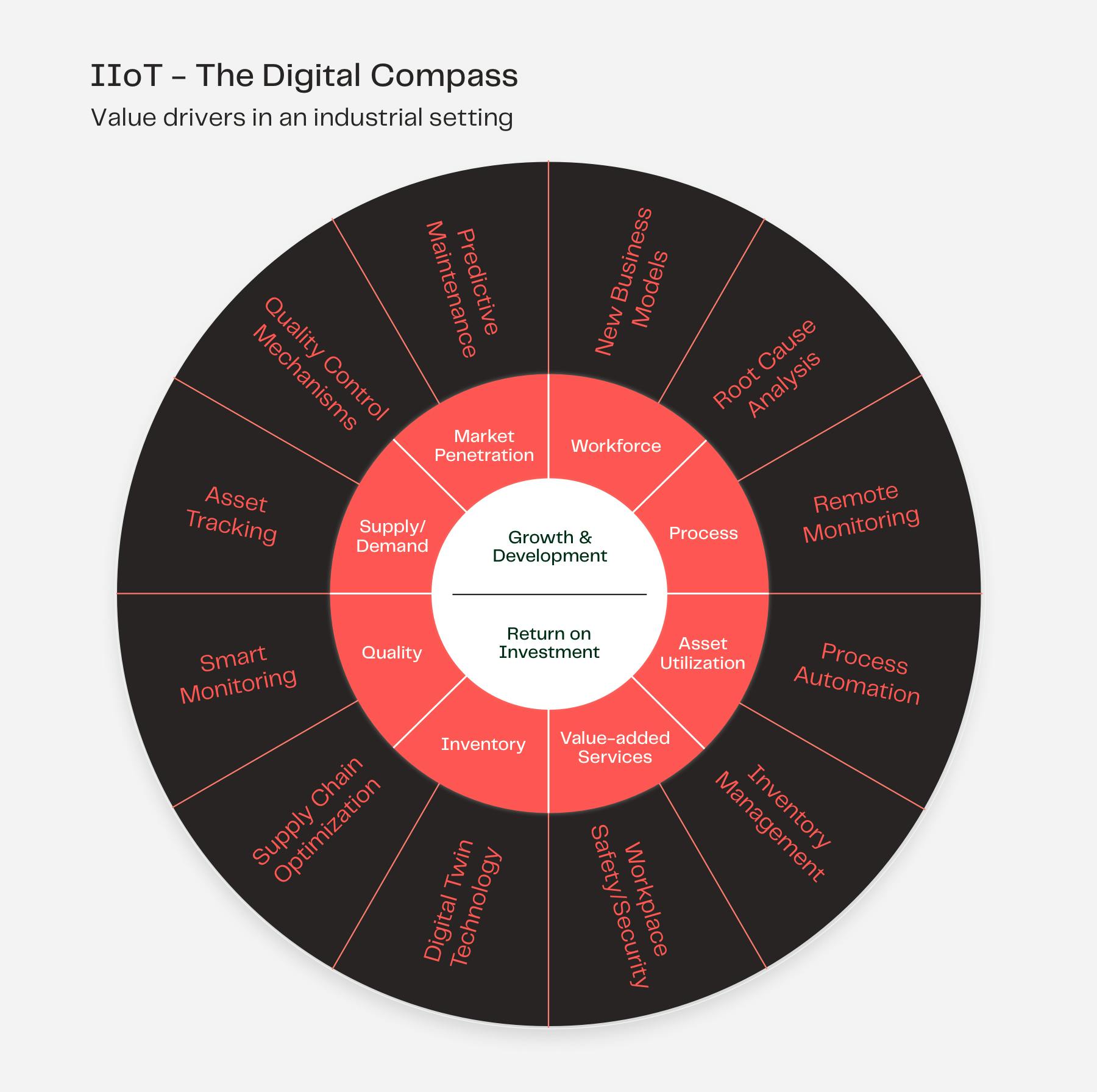
Use Case #1: Root Cause Analysis
Root cause analysis (RCA) identifies the origin of problems in factories or with machinery and then develops a plan of action to solve these problems. RCA offers greater access to equipment data that tracks and records patterns, enabling organizations to learn from insights to support operational and tactical business decisions in real-time. These trends are analyzed to spot anomalies in the manufacturing process where production slows down, drops in quality occur or there’s a decrease in the overall equipment effectiveness (OEE).
By combining industrial IoT and AI, RCA can be automated based on data immediately received from the production process. RCA is based on the principle that effective management is more than merely addressing problems that arise, but rather finding a way in which to prevent them by forecasting the future.
Use Case #2: Predictive Maintenance
Predictive maintenance technologies track all the workings of machinery across the manufacturing process. Manufacturers use this overview to reduce the chances of system failure and equipment degradation. According to Information Technology Intelligence Consulting, 98% of organizations state that a single hour of downtime costs them over $100,000. Therefore, it remains a key priority for manufacturers to ensure that all equipment functions optimally through the application of predictive maintenance.
Real-time data from equipment assets enables manufacturers to forecast maintenance needs long before a problem arises. Due to significant advances in IoT and machine learning, applications with complex algorithms are now in place to make predictions and decisions based upon new data without the need for human involvement. In fact, McKinsey reported that sensor data used to predict equipment failure in the manufacturing environment can reduce maintenance costs by as much as 40% and cut unplanned downtime in half.
Use Case #3: Supply Chain Optimization
In its most basic form, the supply chain consists of a variety of equipment assets and transportation mechanisms operating in sync with one another. As the supply chain becomes more complex with additional components at each stage, it has become increasingly difficult to streamline this process. This is where IIoT offers a solution that enables each component and machine to ‘communicate’ with one other — M2M communication — to perform automated tasks based on data received at each entry point within the supply chain.
Sensors monitor these activities across the supply chain, providing access to real-time information by tracking inventories, timelines for material and resource availability, equipment performance, and tasks in progress.
Use Case #4: Digital Twins
Digital twins are digital replicas of a process, product, or service. A virtual model is created using computer-aided engineering and is integrated with IoT, machine learning, and big data analytics that merge real-time data from its physical counterpart onto an interactive visual interface. This pairing of the virtual and physical worlds allows for the analysis of data to identify any problems before they occur, preventing downtime and forecasting the future through the use of digital simulations.
IIoT offers an end-to-end information flow that highlights key insights across the entire product lifecycle and value chain. As more “things” become connected to the Internet, having a digital equivalent gives manufacturers key insights to advance operational excellence and create other what-if scenarios to determine business outcomes before execution.
Use Case #5: Asset Tracking
With IoT-enabled asset tracking sensors, manufacturers are able to remotely track equipment and transportation fleets in real-time. This enables companies to reduce risk, save money, and have theft prevention mechanisms in place. Leveraging sensors improves manufacturing management and reduces the operational costs of a factory. By using tags and sensors to monitor facilities, organizations gain key insights on how to optimize space usage and production performance.
Radio Frequency Identification Tags (RFID tags) are the sensors used to track vehicles and merchandise, transmitting information to an RFID computer program for organizations to have oversight on each of their assets. Vehicles can also be tracked through an Electronic Logging Device (ELD), which attaches to a commercial motor vehicle (CMV) that synchronizes with the engine to electronically and accurately record all vehicle movements and driving activities.
Use Case #6: Inventory Management
IoT systems in manufacturing lower inventory carrying costs and reduce inventory management errors. Embedded sensors and smart inventory management are catalysts for driving real-time visibility across inventory systems, warehousing, production cycles, and distribution centers.
Beyond this, smart inventory management offers manufacturers real-time actionable insights that can improve the allocation of raw materials, efficient scheduling, transportation logistics, and ordering timelines.
Use Case #7: Quality Control Mechanisms
Quality control (QC) and validation mechanisms often contribute significantly to the total cost incurred by a company. As a result, quality control best practices suggest that organizations should monitor the production process itself, rather than wait until there is a finished product.
IIoT enables connected machines to ensure that quality standards are consistent with mechanisms in place for quick reactions to any issues with the quality of raw materials, processes, or finished products.
Use Case #8: Smart Monitoring
Smart sensors monitor machinery and factories in real-time to provide actionable insights that can be used to improve customer experience, address operational setbacks, and maximize IoT opportunities.
Smart sensor readings are connected to an application dashboard that visualizes data gathered from machinery, detailing any performance anomalies and alerting manufacturers of any urgent issues. Smart monitoring practices enable businesses to reduce maintenance costs, improve processes, strategically plan for the future, and utilize energy more efficiently.
Use Case #9: Remote Monitoring
In the industrial sector, it can be expensive and risky to monitor equipment out on the field without any mechanisms of remote monitoring in place. As a result, manufacturers have begun to implement environmental sensors to continuously monitor external conditions and alert management when quality thresholds or parameters are not met.
By deploying IoT-connected sensors, manufacturers are able to have a live overview of the production process and machine performance. Based on this data, operations can then be adjusted remotely according to the specific needs of the business at any given time within the growth cycle.
Use case #10: Process Automation
Process automation is largely facilitated through the implementation of robotics. In 2025, the projected global revenue from robotics within the industrial sector is set to reach $210 billion.
Industrial IoT offers an effective inventory method called just in time (JIT) manufacturing, whereby materials and goods are scheduled to arrive or be replenished exactly when needed during the production process. This method can drastically optimize an organization’s productivity levels, capital allocation, and reduces manufacturing waste. However, organizations are then generally required to forecast demand accurately. Automating processes that would otherwise require human involvement to improve efficiency and save time are among the most common reasons for deploying IoT into the industrial sector.
Use Case #11: Workplace Safety and Security
Accidents and risk management within factories still remain a significant challenge for employers. As a solution to this, IoT technologies such as video monitoring and remote monitoring can help improve employee safety and security. IoT devices can optimize worker safety and security by monitoring specific key data indicators such as employee absences, property or vehicle damage, and any additional losses or damages that may occur during regular business operations.
Sensors can also accurately monitor temperature, humidity levels and can detect other environmental conditions that may cause harm to employees. Methods can be put in place so that the data from worksite sensors deliver fast and accurate messages to emergency services in the case of a disaster.
Use Case #12: New Business Models
With IoT-backed solutions, manufacturers are transcending product-based business models into services-based models to create new opportunities across the value chain. Smart connected products are rich in untapped data and revenue potential which has opened up new ways for the manufacturing and industrial sectors to conduct business — by using servitization to innovate new offerings.
One of the most exciting things about IoT is that business value can be created far beyond the problem that IoT was originally meant to solve.
From Smart Components Toward Smart Organizations
There are many reasons for putting industrial IoT standards in place, but it mainly comes down to a few driving forces: efficiency, cost reduction, risk management, and enhanced value streams.
Looking at the enterprise infrastructure, initial implementations of IIoT begin with applications of smart sensors before scaling up and transitioning into smart organizations, which use data-driven insights to drive more sustainable, resilient, and efficient processes.
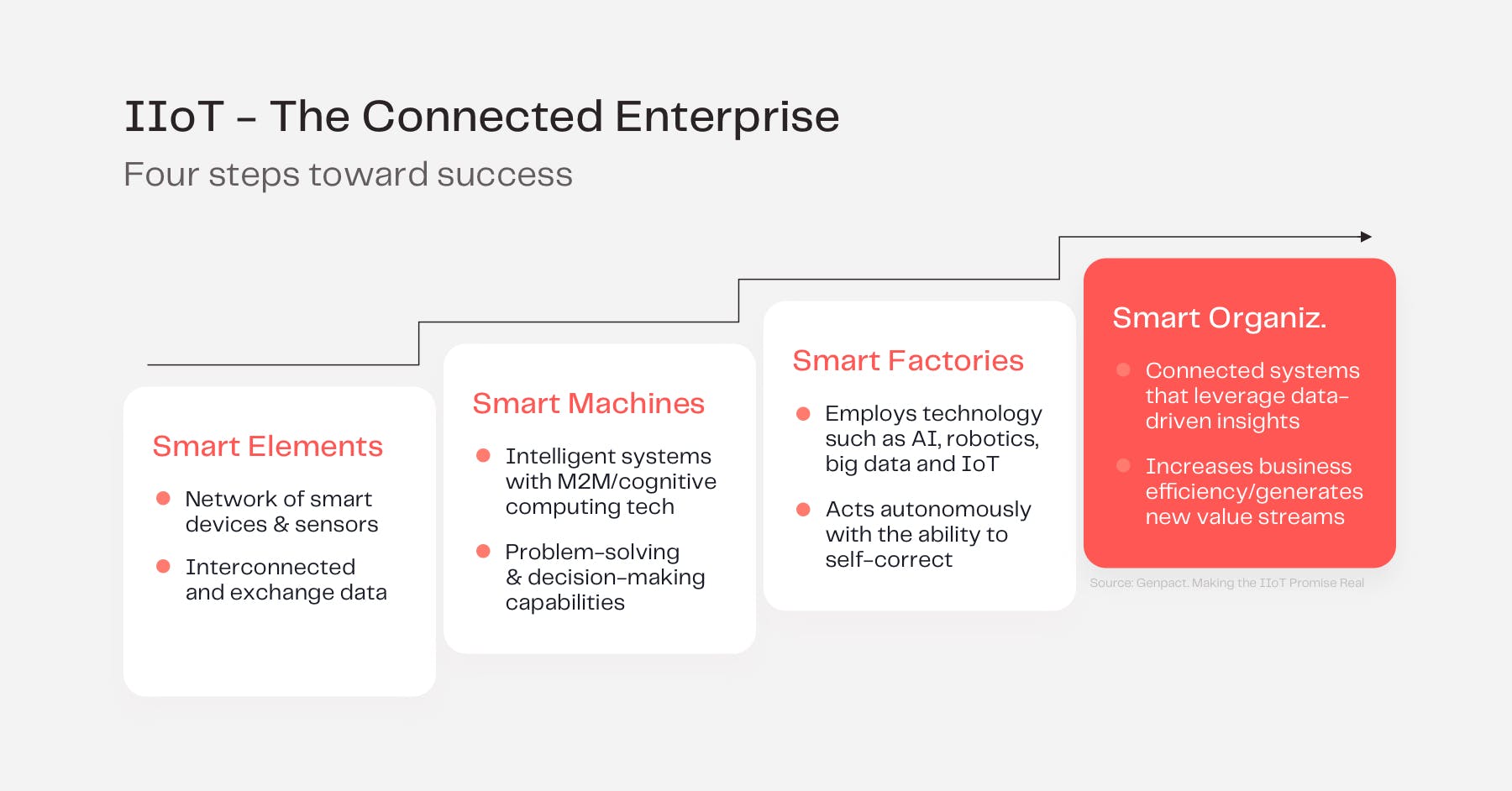
Smart manufacturing enables organizations to identify opportunities to automate operations and leverage data analytics to improve overall production performance. Connected machines can effectively communicate with one other, supporting greater levels of autonomy in the production process.
Organizations that prioritize applications of IIoT are well prepared to progress in the inevitable Machine Economy of the future.